Project Cost Engineering
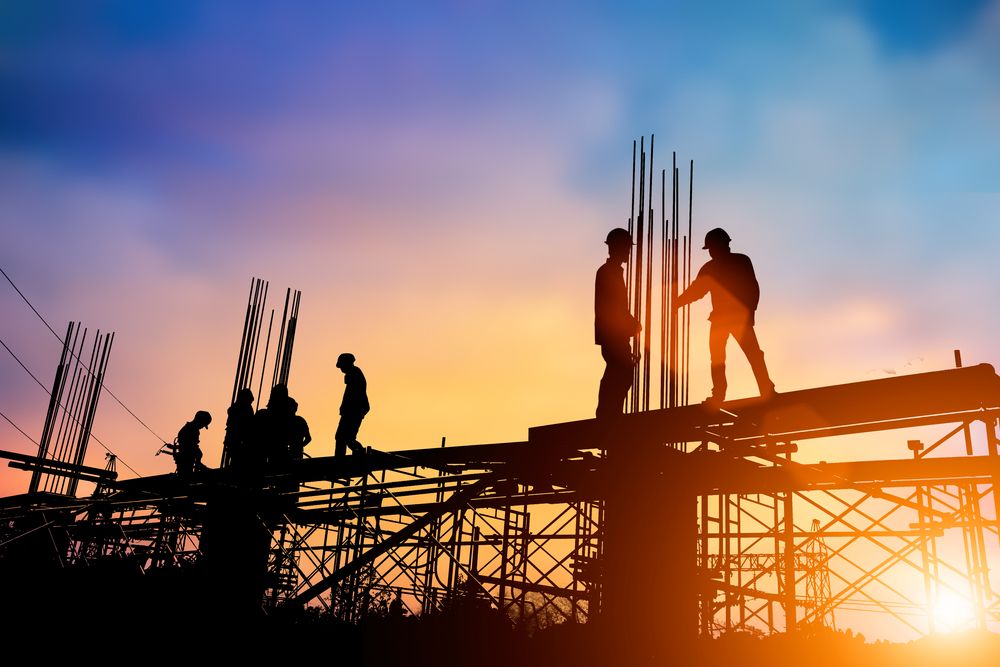
- Cost benchmarks and analyses for engineered components, based on our deep knowledge of technical products and services, and our databases of materials costs for major factor inputs such as materials, labor, and energy
- Benchmarks against similar projects
- “Fitting” the cost of major components (such as hydrocracking reactors) to the specific engineering requirements (often size, material, and pressure) of each project based on our proprietary databases
COST ESTIMATES
Parametric cost analysis allows buyers to adjust the price bids to varying component engineering specifications, particularly to varying size, pressure, temperature, and material characteristics. Our Cost Baselining reports are full-text, and include extensive data workbooks that allow buyers to experiment with different assumptions regarding engineering specifications, number of units purchased in the same order, location of manufacture, and more
Cost Benchmarks, Cost Ranges, and Cost Calibrations
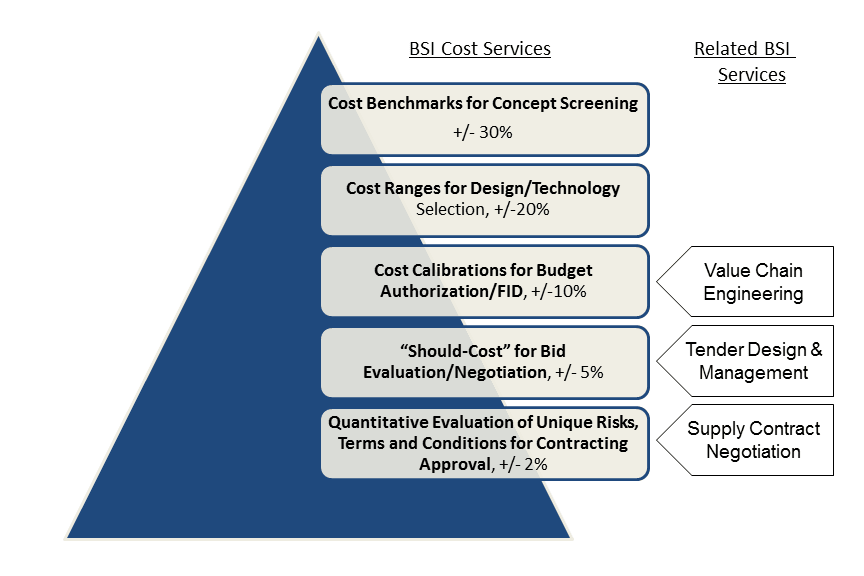
Each engagement facilitates an important decision-making process in the project lifecycle.
CASE STUDIES
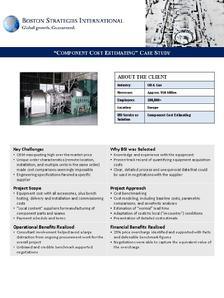
- Industry: Oil and gas
- Key Challenge: Foreign EPC firms submitted excessively high bids
- Why BSI was Selected: Expertise in pipeline construction, cost benchmarking, and cost modeling
- Project Scope: Engineering, procurement, and construction costs
- Project Approach: Benchmarking and cost modeling
- Operational Benefits: Increased local content
- Financial Benefits: Decrease in project costs
Click here to read the full case study.
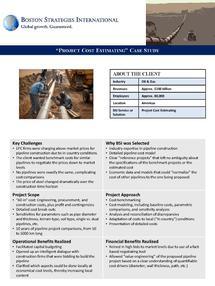
- Industry: Oil and gas
- Key Challenge: Foreign OEM submitted an excessively high bid
- Why BSI was Selected: Expertise in the equipment type, cost model, and benchmarks
- Project Scope: Equipment plus accessories, testing, installation, commissioning, and spares
- Project Approach: Benchmarking and cost modeling
- Operational Benefits: Allowed the procurement team to stay focused on executing the project on-time.
- Financial Benefits: 25% overcharge identified
Click here to read the full case study.
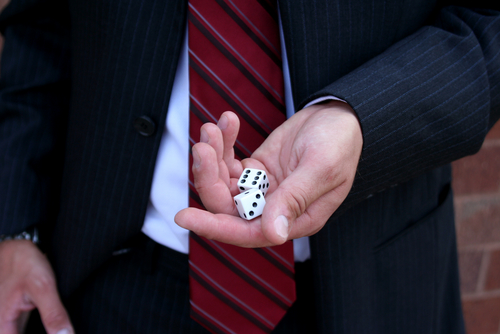
Budgeting for Volatility
Recent raw material price volatility has hit budgets hard. Prices of metals, wood products, paper, packaging, and fuel — just to name a few commodity-based materials — have all increased markedly. Labor costs may be the next to take off. This study explores how best-in-class companies are adjusting their procurement and budgeting practices to cope with today’s economic volatility. This session will outline conventional as well as innovative tools and processes that leading companies are using to manage volatile prices and material unavailability.
Please click here for the slide presentation excerpt.
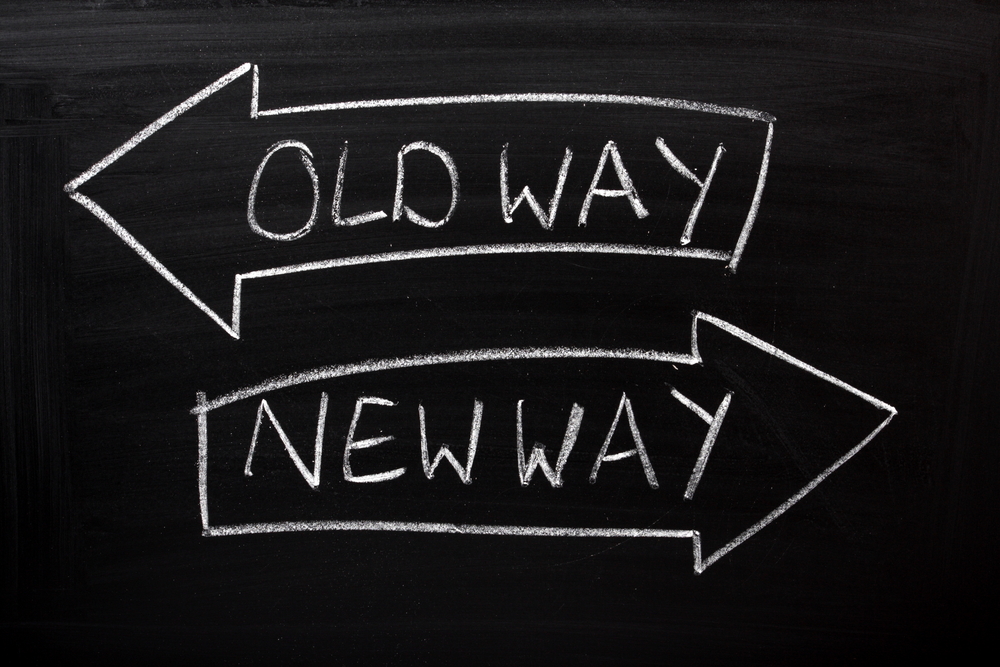
Supply Risk Management
While many purchasing groups have reduced the number of suppliers they buy from and increased the average length of contracts, few of them have much forward visibility into the markets in which they are taking such positions. Making long-term commitments without corresponding market analysis is perilous, since market prices may swing above or below today’s levels and the longer the agreement, the greater the possible budget variance. This presentation will examine how leading companies use forecasts and market outlooks to make long-term decisions that involve investment and risk.
Please click here for the slide presentation excerpt.
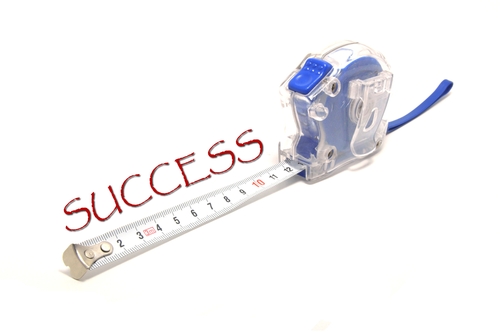
Metrics: From Information to Strategy
The increasing amount of data that is available is changing the way managers can and do measure our business performance. How does technology assist in compiling, visualizing, managing data, and how can it help link supply chain initiatives to the balanced scorecard?
Presented to PMAB, 2007.
Please click here for the slide presentation excerpt.
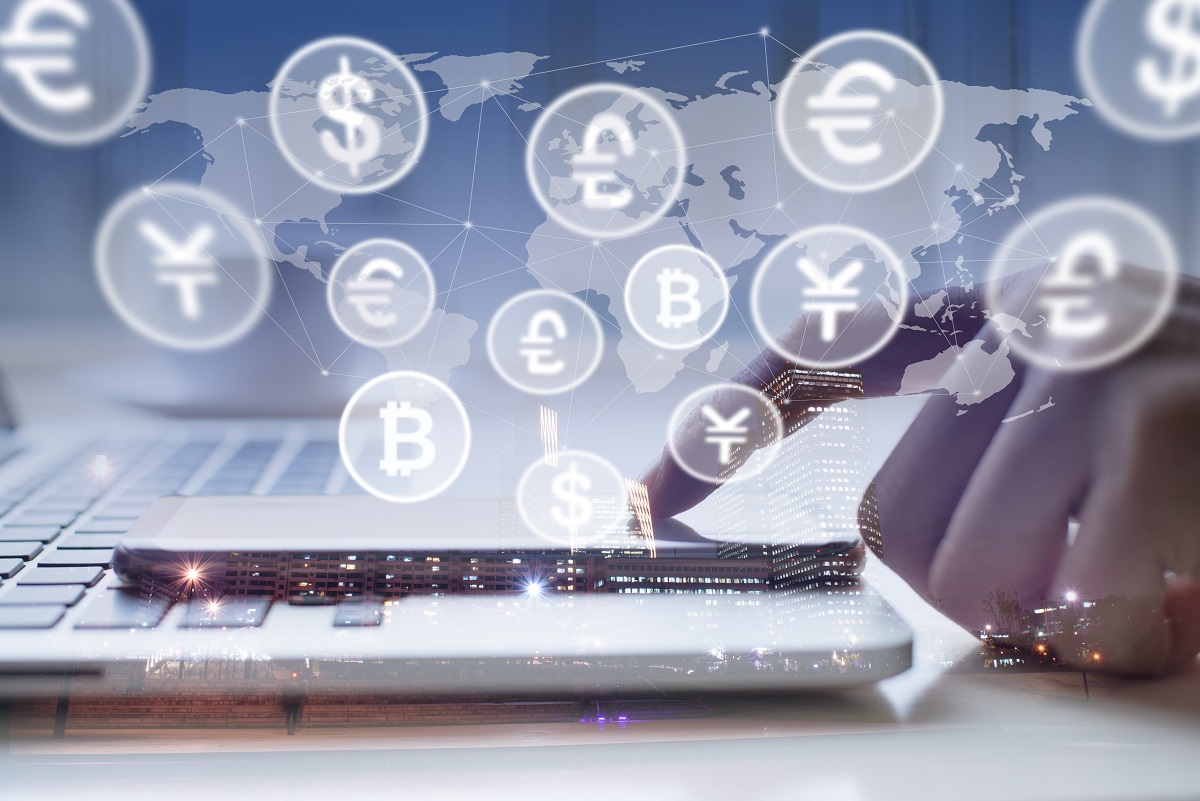
Measuring Sourcing Performance
Getting performance out of sourcing truly is a matter of life or death for most companies. It’s strategic for any low-cost business and for any firm that claims supply chain management as a core competency. It provides robust financial leverage and is a juicy target for P&L and stock-price enhancement for public companies.
Please click here for the article.
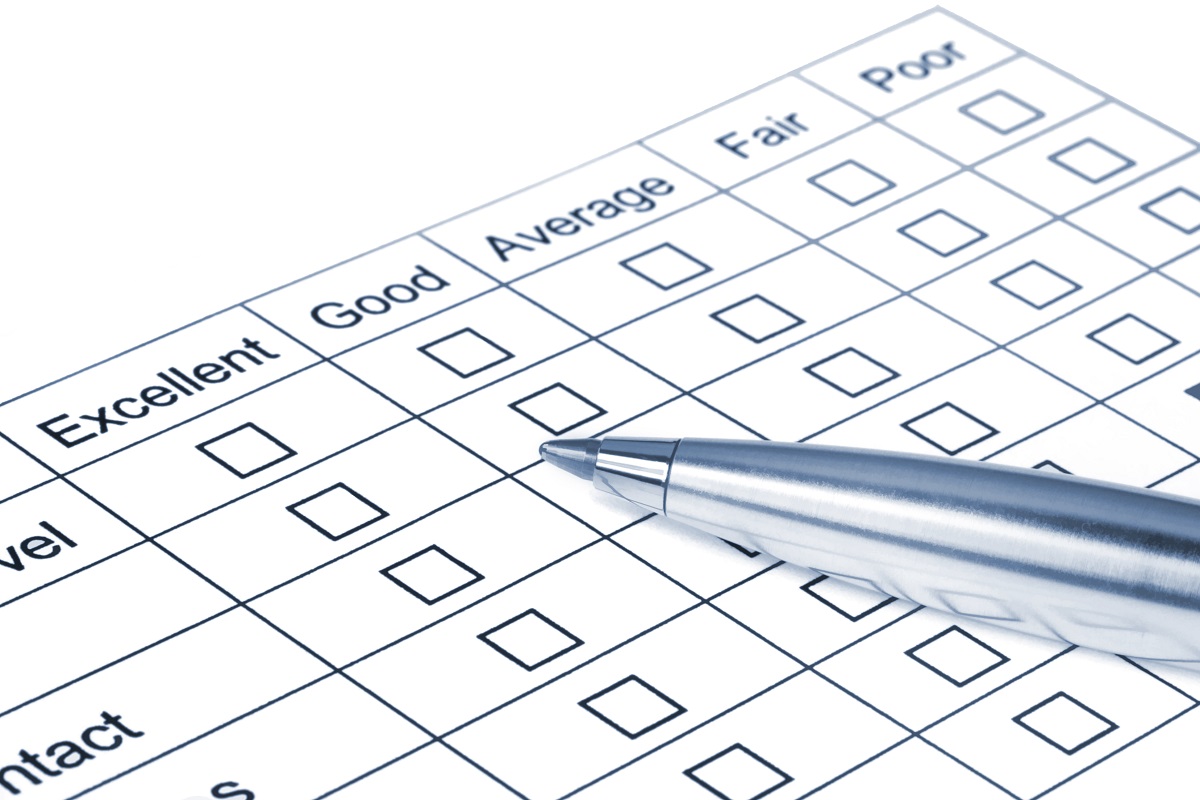
Supply Chain Report Card
During periods of dramatic change like we have experienced in the recent economic recession, 20 percent of all people shift jobs. At least that is what my e-mail box tells me based on the frequency with which e-mails bounce, and that is consistent with the turnover experienced in the 2000-01 recession.
Please click here to download the article.